Several plastics meet regulatory requirements for limited contact devices, or medical devices that can be in contact with bodily tissue and fluids for up to 24 hours. These medical grade polymers, and the devices in which they are used, satisfy specific ISO 10993 biocompatibility standards for these types of applications.
Certain medical grade plastics are available in transparent and opaque versions to serve different application requirements. Custom tints and opaque colors are also options, and can be beneficial for such reasons as visually differentiating instruments in surgical kits.
While they have biocompatibility compliance in common, the physical properties of these polymers vary significantly, as does their tolerance to sterilization methods and media.
This overview compares four high-performance medical grade plastics that are specified for various transparent devices, their property differences, and their unique advantages for different types of applications.
What is a High-performance Medical Grade Plastic?
Designers have several options in transparent plastics for limited contact devices, or those that can be in contact with bodily fluids and tissue for up to 24 hours. Some of these polymers are intended for single-use applications and cannot withstand repeated sterilization without losing important physical properties, and often their transparency as well. High-performance polymers, conversely, retain high their high strength, rigidity, durability and biocompatibility after exposure to several cycles in typical sterilization processes. As a result, these high-performance medical grade plastics are specified for a range of devices intended for repeated sterilization and re-use.
What High-performance Medical Polymers Are Commonly Used for Transparent Devices?
Four transparent biocompatible polymers provide different combinations of properties that cover the broad range of performance requirements for transparent multi-use devices. All are melt processable, and all have been used for numerous applications that require compliance to standards for limited contact with bodily tissue and fluids for up to 24 hours (Table 1).
Radel PPSU (polyphenylsulfone)
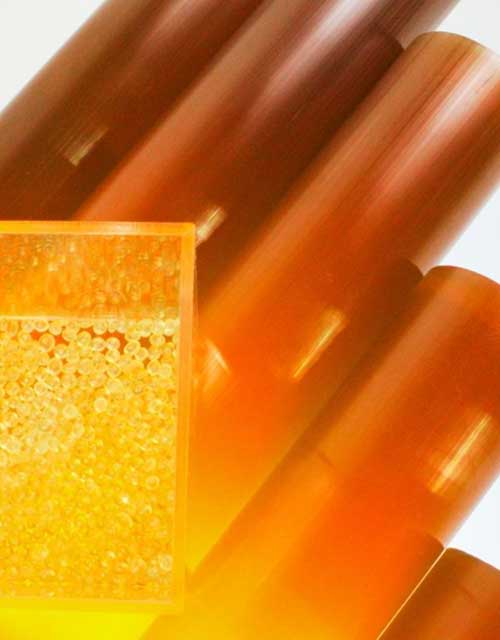
PPSU, widely recognized under the Radel tradename, is a member of the sulfone family of amorphous thermoplastics. The natural polymer is transparent amber, and is available in custom tints. The polymer is also offered in opaque healthcare colors, which are specified for medical device applications such as color-coded sizing trials for total joint arthroplasty surgical sets, and surgical instrument handles. Device components can be injection molded and also machined from extruded stock shapes.
An exceptional feature of PPSU is its tolerance to steam sterilization. The polymer maintains its physical properties after as many as 1,000 cycles in 134o C steam, outperforming all other medical grade plastics. In addition, it is compatible with all other common sterilization methods. Another attribute of PPSU is its impact resistance, which rivals polycarbonate’s and exceeds the that of the other high-performance medical grade plastics.
The mechanical properties of PPSU, specifically its flexural modulus and tensile strength, are also well-suited to transparent medical device applications where the polymer’s stiffness coupled with its intrinsic ductility are desirable.
Ultem PEI (polyetherimide)
Commercially available as Ultem PEI, the natural polyetherimide polymer is dark amber, and exhibits good transparency especially in thin-walled injection molded medical devices. Stock shapes extruded from Ultem are also available for machining production and prototype parts.
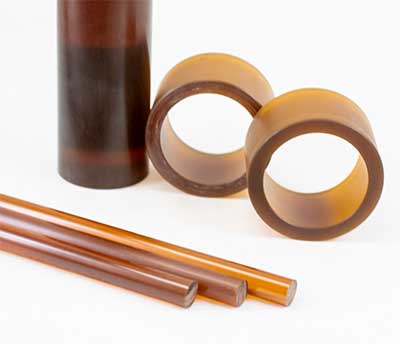
Among the high-performance medical plastics, PEI ranks at the top level of mechanical strength and structural rigidity, as measured by ASTM and ISO flexural and tensile testing. With the polymer’s glass transition temperature (Tg) or softening point of over 200oC, devices made from PEI easily withstand steam sterilization temperatures without distorting.
Ultem HU 1000, the standard medical grade, is less tolerant to repeated cycles in steam than sulfone polymers. However, a transparent PEI polymer blend designated Ultem HU 1004 offers improved tolerance to steam sterilization as well as higher impact resistance. Both Ultem PEI grades perform well in all other sterilization methods.
The PEI polymer has intrinsically good chemical resistance to hospital chemicals and sanitizers. However, like any polymer, it has its limitations, and designers should consult with the material supplier regarding compatibility with specific chemicals.
Polysulfone (PSU)
Natural polysulfone polymer has a very light yellow tint, making it a good candidate for medical devices that require a high degree of transparency, especially in heavier wall thicknesses. Its mechanical strength is similar to that of PPSU, also a sulfone polymer.
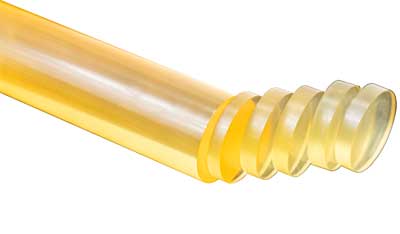
Polysulfone readily withstands exposure to all common sterilization methods. Its hydrolysis resistance and glass-transition temperature or softening point of 185oC afford dimensional stability and longevity for devices after repeated exposure to 134o C steam sterilization. Among the high-performance transparent medical plastics, only PPSU withstands a greater number of autoclave cycles.
The polysulfone polymer offers good ductility as well as rigidity, an advantage for devices that may be flexed for assembly or removal from a fluid transfer system. As with all the high-performance medical plastics, polysulfone has its unique chemical resistance profile, and the material supplier is the best source for information on compatibility.
Polysulfone can be injection molded into clear precision device components, and is available in the form of stock shapes for machining of prototype and production parts.
Polycarbonate (PC)
The most notable properties of polycarbonate are its high impact resistance and transparency, which have made polycarbonate sheet a leading material for protective glazing in damage-prone window systems. Various grades are also injection molded into impact-resistant automotive and industrial components.
Developments in medical grade polycarbonate resins include a family of Makrolon Rx branded resins. All have similar physical properties, and differ mainly in processing characteristics. Makrolon Rx 3440 and Makrolon Rx 1805, for example, are high viscosity medical grades, while Makrolon Rx 2530 and Makrolon Rx 2440 are medium to low viscosity resins. Most grades are suitable for injection molding only, but stock shapes for machining parts and prototypes are also available from specialized medical polymer extruders.
Devices made from polycarbonate can be sterilized by gamma radiation and ethylene oxide, but the polymer withstands fewer cycles than the other high-performance medical plastics covered in this overview. It is not recommended for autoclaving in steam at 134o C, or for more than one cycle at 121o C. Repeated steam sterilization can cause polycarbonate to embrittle or craze. It’s heat distortion temperature of 126o C is also insufficient to prevent distortion in devices subject to the higher sterilization temperature.
What are Typical Applications for Transparent High-Performance Medical Plastics?
Transparent medical plastics provide visibility for monitoring the level or flow of fluids and drugs. They are also specified for clear devices with internal lighted sensors that indicate proper functioning. High-performance medical plastics such as polysulfone, PEI, PPSU and PC offer the advantage of reusability because of their tolerance to repeated sterilization (Table 2). While these polymers carry a premium for performance compared to disposable or single-use commodity plastics, their longevity in sterilization media typically provides economic advantages that offsets their initial cost.
Each of the high-performance transparent medical grade plastics provides a unique combination of performance attributes as shown in Table 1. The choice of material hinges on the functional requirements that dictate the toughness, durability, rigidity, and temperature resistance required, as well as longevity based on the expected number of sterilization cycles.
Transparent medical devices and related multi-use healthcare applications where these high-performance sterilizable medical grade plastics are used include:
- Drug delivery system components
- Fluid transfer valves
- Ricordi chambers
- Autoclavable instrument trays and carriers
- Electronic sensor housings
- Slide and test tube carousels
How are High-Performance Medical Plastics Converted into Devices?
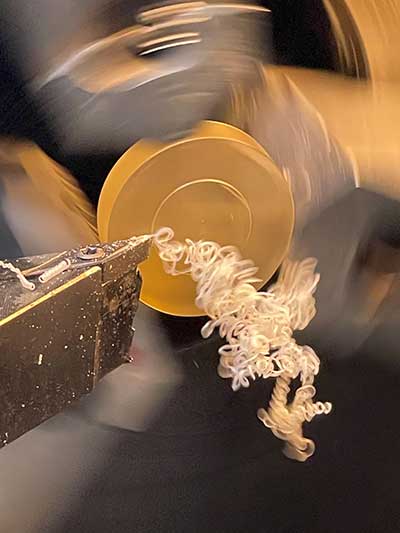
A major intrinsic benefit of high-performance polymers is their melt processability by injection molding and by extrusion. The injection molding process yields highly consistent repeatability from part to part in high volume production, and does so economically. Melt extrusion is a process for producing stock shapes, that are then machined into prototypes for design validation.
Machining stock shapes is also an option for producing highly complex parts that may not be possible with injection molding. Additionally, post-machining can add design features to molded parts that injection molding alone cannot achieve.