Home - Implantable Genesis PEEK for Medical Device Designs - Implantable Genesis PEEK Semi-finished Shapes
Biocompatible GENESIS PEEK machinable shapes are extruded under process conditions that optimize properties and consistency in implantable medical device prototypes and production parts.
Medical Device Industry Recognition of Implantable PEEK
The development of biocompatible PEEK grades enabled the medical industry to capitalize on the benefits of the polymer for a wide range of implantable devices. Decades of successful applications in millions of devices worldwide confirm its viability and have established it as the material of choice over metals for many critical products.
PEEK Polymer’s Melt Process Versatility
Major PEEK suppliers provide pelletized implantable PEEK resin as the raw material for melt processes that best serve different production quantity and part design requirements:
- Injection molding – Ideal for high volume production of precision parts.
- Film processing – Yields thin gauge PEEK for fabricating intricate components.
- Melt extrusion – Provides the shapes needed for precision machining of prototypes, mid-range production quantities and part designs too complex for injection molding alone.
Genesis Process Capabilities in Biocompatible PEEK
Genesis converts our MDM customers’ implantable PEEK using all three melt processing technologies, and also machines precision components from extruded shapes. As a result, customers can transition through the product life cycle with Genesis, from early-stage medical device prototypes during product development to high volume production of finished components.
In addition to these custom conversion capabilities, Genesis has also developed implantable Genesis PEEK film and Genesis PEEK machinable semi-finished shapes as standard products.
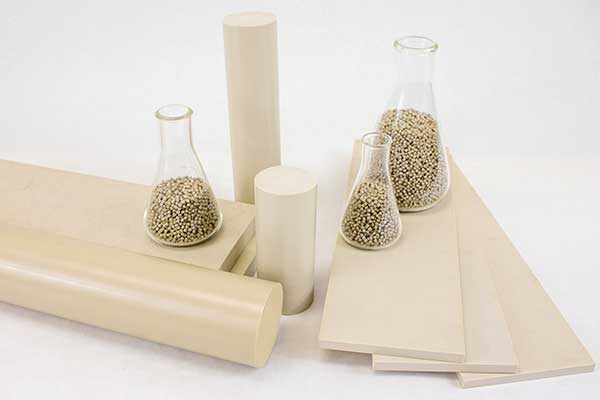
Genesis PEEK Semi-finished Shapes
In response to MDMs requiring a qualified and capable source of implantable PEEK shapes for precision machining, Genesis now offers Genesis PEEK in a versatile range of standard rod and plate sizes. Short delivery lead times facilitate quick turn-around when needed for medical device prototypes and production quantities. In addition, custom rod diameters and plate thicknesses are available in reasonable minimum order quantities. This capability provides customers with highly efficient sizes that minimize material loss during machining.
Standard rod diameters (mm):
- 6; 16; 20; 25; 30; 40
- Other diameters made to order
Plate thicknesses (mm):
- 4mm – 25.4mm
- Larger thicknesses on request
- Maximum width 610mm
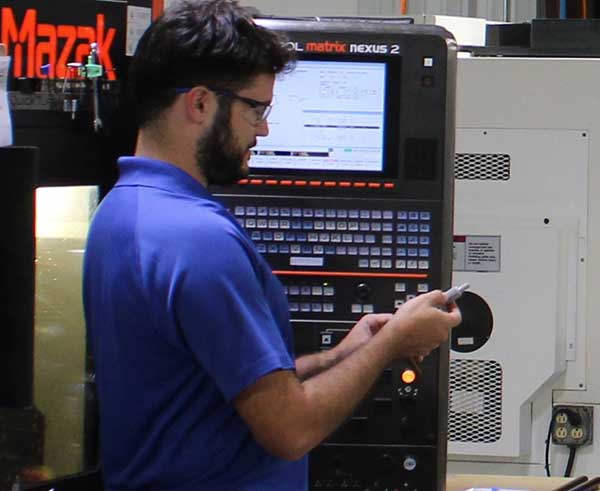
Equipment and Process Parameters Developed for PEEK
Genesis engineers designed our extrusion equipment and defined the specific process conditions that are ideal for the production of Genesis PEEK semi-finished shapes. These dedicated investments coupled with years of process experience translate to consistently high quality and performance in machined components for implantable medical devices.
How PEEK Properties Benefit Medical Device Applications
The performance attributes inherent in the PEEK polymer are reflected in the implantable grade of the resin and in Genesis’ PEEK shapes extruded from the material (Table 1). The benefits of its properties also translate to components that are precision-machined from Genesis PEEK rod and plate:
- Compatibility with steam, ethylene oxide (EtO) and gamma irradiation sterilization
- Retention of physical properties and biocompatibility after repeated sterilization cycles
- Radiolucency for accurate imaging by X-ray, CT and MRI
- Excellent tensile strength, rigidity and toughness
- Flexural modulus similar to cortical bone with reduced stress shielding
- Resistance to fatigue and creep after repeated load and flexing
- Resistance to an exceptionally wide range of chemicals
- Very low levels of extractables and leachables
- No risk of allergic reactions associated with some metals
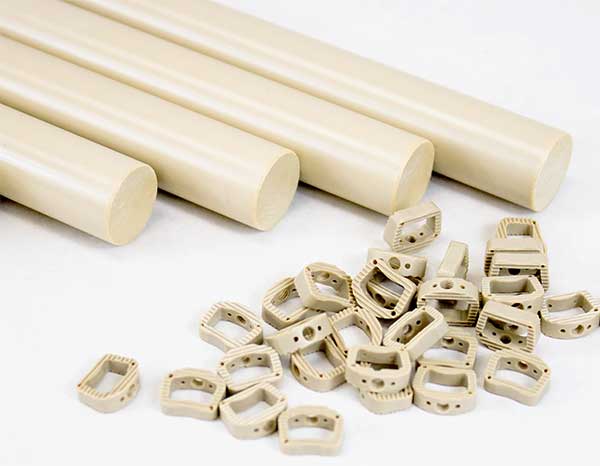
Table 1: Properties vs. ASTM F2026-17 Standard
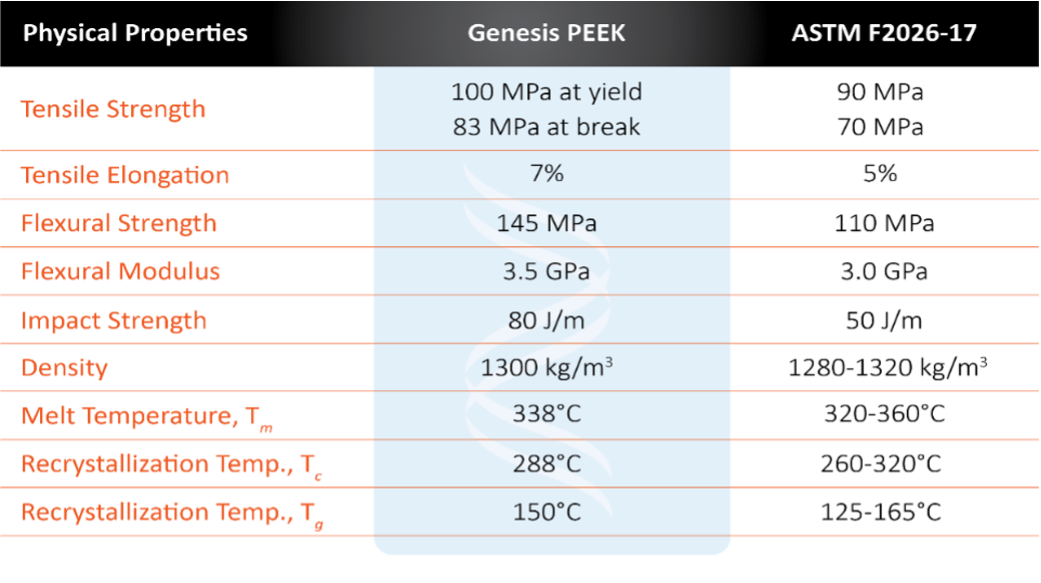
Genesis PEEK rod and plate products comply with the medical industry’s ASTM F 2026-17 standard for implantable materials. In addition, the quality management system for the Genesis PEEK production facility is ISO 13485:2016 certified and adheres to good manufacturing practices (cGMP) in support of medical device customers’ ability to bring products to market.
Implantable PEEK Resin Standards Compliance
The implant grade PEEK resin used to produce Genesis Implantable PEEK film is compliant with ASTM F2026-17 requirements for mechanical properties and biocompatibility. The resin manufacturer is also ISO 13485:2016 certified and adheres to current Good Manufacturing Practices (cGMP).
How Versatile Production Capabilities Benefit MDMs
Genesis Medical Plastics’ versatile manufacturing capabilities afford MDM customers several benefits through the phases of their device’s life cycle:
- Reasonable custom size minimums to support product development
- Machining capacity for prototyping and production parts
- The flexibility to extrude efficient rod diameters and plate thicknesses that eliminate material waste during machining
- In-house injection molding for easy conversion when production quantities support the required tooling investment
Millions of successful applications validate the ability of biocompatible PEEK to meet the demanding regulatory and functional requirements of implantable medical devices. Genesis PEEK shapes offer opportunities for producing prototypes and intricate machined components for these and other implantable medical devices that require contact with bodily fluids, bone and tissue for more than 30 days:
- Spinal interbody fusion cages
- Spinal stabilization rods
- Suture anchors
- Dental implants and prostheses
- Trauma fixation plates
- Cranio-maxillofacial (CMF) implants
- Femoral implants
- Total and partial joint replacements
- Cardiovascular implants
- Intramedullary implants
- Bioelectronic device components
- Drug delivery systems
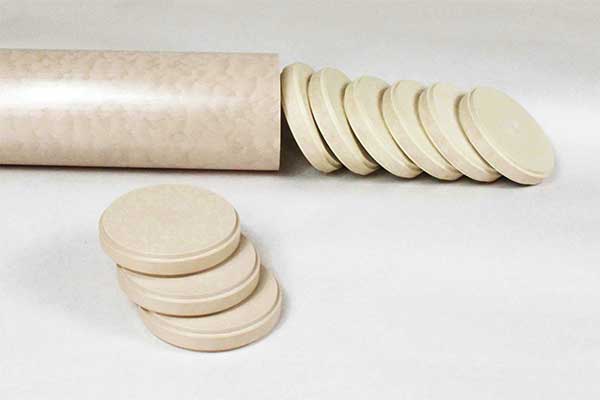
Near-net Shapes as a Cost-effective Bridge from Machining to Molding
In addition to extruded semi-finished shapes, Genesis Medical Plastics can also injection mold near-net shapes that approximate a component’s configuration. The close-to-size blanks can be produced in lower cost molds, then quickly finish-machined to exact design dimensions.
The technique provides device manufacturers with an efficient interim transition step from machining for intermediate quantities until production volumes justify an investment in high quality injection molding tooling. Depending on part design and unit volumes, the typical benefits compared to machining include lower material costs and higher production quantities in shorter manufacturing turn-around times.