Genesis-engineered extrusion, injection molding and machining equipment has the proven versatility to convert the diverse spectrum of medical grade and biocompatible plastics into the semi-finished shapes and components our customers require.
Genesis’ Growing Portfolio of Medical Plastics
Genesis extrudes, injection molds and machines numerous rigid medical polymers and continually works with major resin suppliers and customers on new grades and formulations. Widely specified polymers and brands include:
- PEEK (polyetheretherketone) – VictrexTM PEEK; KetaSpire® PEEK; Vestakeep® PEEK
- PPSU (polyphenylsulfone) – Radel® PPSU
- PEI (polyetherimide) – UltemTM PEI
- PSU (polysulfone) – Udel® PSU
- PARA (polyarylamide) – Ixef®; single-use applications.
- PC (polycarbonate) – Lexan® PC
- POM-C (polyoxymethylene; acetal copolymer) – Celcon® POM-C; Ultraform® POM-C; Hostaform® POM-C
- PP-H (polypropylene homopolymer) – multiple brands
Medical Plastics Tailored to Application Requirements
The range of medical plastics Genesis converts into machinable shapes and parts provides device manufacturers with the ability to fine-tune the performance and economics best suited to their application. To satisfy different device requirements, designers have options on such performance factors as:
- Longevity in various sterilization processes
- Durability, toughness in use; break-resistance
- Resistance to chemicals, cleaners and sanitizers
- Structural strength, rigidity
- Resistance to distortion or deforming at high temperatures
- Transparency, opacity and colorability
- Wear resistance in moving parts
Medical plastic resin producers also offer grades with additives such as fiber reinforcement that add strength, and lubricants that improve wear resistance. Custom colors are also available with most resins.
Biocompatible Plastics for Short-term Internal Contact Applications
Several factors determine biocompatibility of plastics used in devices that are in contact with internal body tissue or fluids. A key factor is the length of contact time.
Biocompatible plastics for implantable devices, for example, are generally defined as suitable for contact with internal tissue or fluid for longer than 30 days. The field of polymers in this long-term contact category is relatively limited.
A greater number of plastics have proven their biocompatibility for devices that have short-term contact ranging from a few hours or less, up to the 30-day benchmark. Plastics commonly specified for these applications include Radel PPSU, POM-C, polysulfone, PEEK and Ultem PEI. Genesis can provide more details on these types of polymers based on our application experience, and through our working relationships with the resin suppliers.
It should be noted that some plastics used in short-term contact applications – most notably PEEK – have counterparts within the same polymer family that are used in implantable applications. However, the implantable grades differ significantly in how they are produced, supplied and branded.
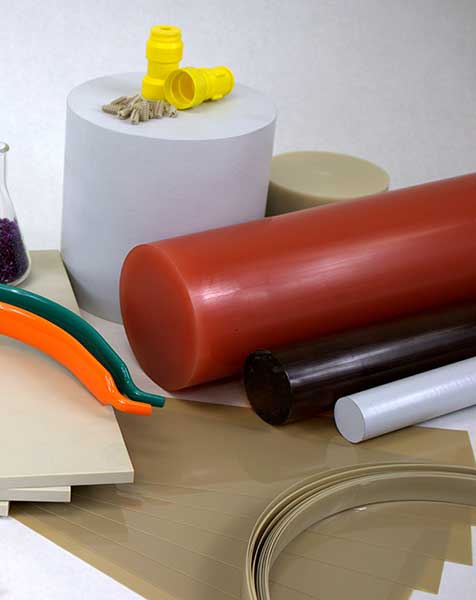
Custom Medical Plastics Formulations
Device manufacturers often work with specialized medical plastics compounders to develop proprietary formulations for new products. Genesis has built a reputation for transforming these often-challenging custom materials into semi-finished machinable shapes, and both machined and injection molded parts. Our successes include machinable shapes extruded from customers’ proprietary formulations with as much as 60% additive content.
Medical Plastics’ Sterilization Resistance is a Key Consideration
Medical grade plastics differ in their tolerance to various sterilization processes. Some polymers excel in all types of sterilization methods. Others withstand only a few specific types for limited cycles, and are completely incompatible with others. As a consequence, a key material specification factor is the medical plastic’s tolerance to both the sterilization process and the number of exposure cycles the health care facility typically employs.
Table 1 approximates the tolerance of widely-specified medical plastics to various sterilization processes and cycles, and can serve as a general guide to help the designer narrow the range of options for an application. In all cases, it is strongly recommended that designers contact the resin supplier through Genesis or directly for definitive information on a material’s suitability for the intended sterilization procedure.
Table 1: Compatibility of Common Medical Plastics with Sterilization Methods.*
Performance key: | Excellent resistance and longevity | Resistant to limited cycles | Minimal or no resistance | |||||
Medical Plastics’ Tolerance: Multiple Cycles* | ||||||||
Sterilization Method: | PEEK | Radel PPSU | Ultem PEI | Udel PSU | PP-H | PC | POM-C | Ixef PARA |
Steam 121°C (250°F) | ||||||||
Steam 134°C (273°F) | ||||||||
ETO 60°C (140°F) | ||||||||
Gamma 23°C (73°F) | ||||||||
Plasma 45°C (113°F) | ||||||||
Hot Air 180°C (356°F) | ||||||||
Hydrogen Peroxide |
*Part design and material grade can affect performance. Testing of actual parts is recommended.
Medical Polymers and Key Physical Properties
The following overviews summarize the key attributes of several medical polymers that are commonly specified for rigid, non-implantable device and instrument components. Table 2 compares significant physical properties often considered for medical devices. In addition to extrusion and parts-production capabilities, Genesis’ technical team offers in-depth information on these and other medical grade plastics to assist designers in narrowing the range of material candidates for their device components.
Test | Units | PEEK | PPSU | PEI | PSU | PP-H1 | POM-C | PC | |
Flexural Modulus | ASTM D790 | Gpa | 3.7 | 2.41 | 3.51 | 2.69 | 2.15 | 2.76 | 2.3 |
ksi | 535 | 350 | 509 | 392 | 313 | 400 | 345 | ||
Tensile Strength
| ASTM D638 | Mpa | 95 | 69.6 | 110 | 70.3 | 35.9 | 65.5 | 70 |
kpsi | 14 | 10.1 | 16 | 10.2 | 5.2 | 9.5 | 10.1 | ||
Tensile Elongation @ break | ASTM D638 | % | 20-30+ | 60-120 | 60 | 30 | 20-60 | 30 | 60 |
Impact Resistance, Notched | ASTM D256 | J/cm | 0.69 | 6.94 | 0.53 | 0.69 | 0.48 | 0.534 | 6.95 |
ft-lbs/in | 1.29 | 12.9 | 0.993 | 1.29 | 0.9 | 1 | 13 | ||
Heat Distortion Temp. @ 264 psi | ASTM D648 | °C | 157 | 207 | 201 | 174 | 71 | 104 | 132 |
°F | 315 | 405 | 394 | 345 | 160 | 220 | 270 | ||
Water Absorption, 24 hrs | ASTM D570 | % | 0.1 | 0.37 | 0.25 | 0.3 | 0.1 | 0.2 | 0.15 |
* Properties based on supplier data for unreinforced resins.
Application-specific testing recommended to verify material suitability.
PEEK (Polyetheretherketone)
PEEK ranks in the top tier of medical plastics on its combination of physical properties and sterilization resistance. The polymer has inherently high flexural modulus or rigidity, and retains its strength even at the highest steam or dry sterilization temperatures. Grades reinforced with carbon or glass fibers offer even greater levels of stiffness when needed for certain medical instruments.
Among medical plastics, PEEK stands out for its imperviousness to a wide range of chemicals, solvents and sanitizers used in health care facilities and medical laboratories. It also provides exceptionally long life for components that are expected to last through many hundreds of cycles in all common sterilization methods. As an example, testing done by one of the major resin suppliers shows that it retains its strength and ductility even after 1,000 autoclave cycles.
Although PEEK is a premium polymer, the initial cost of the resin and the semi-finished shapes or parts made from it can be offset by the material’s proven long-term sterilization life in components and devices.
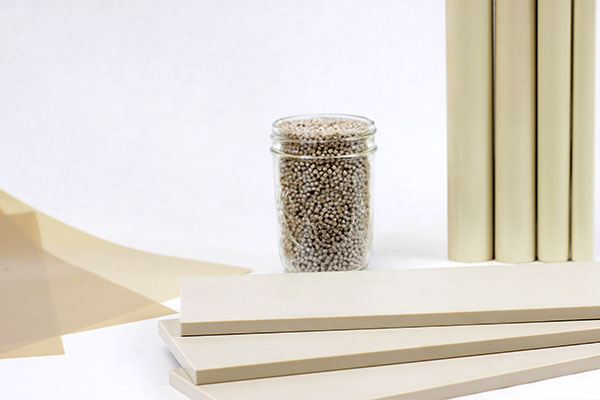
PPSU (Polyphenylsulfone)
PPSU, widely recognized under its Radel tradename, offers excellent resistance to chemicals and high temperatures, and withstands hundreds of cycles in common sterilization processes. Its impact resistance and durability rank higher than PEI and PSU. While not quite at the level of PEEK on sterilization longevity, PPSU performs impressively, with no significant fall-off in properties up to 800 hundred autoclave cycles.
The PPSU polymer has a very light transparent tint and is easily colorable. Solvay offers Radel PPSU in standard health-care colors that are stable through hundreds of sterilization cycles. This allows color-coding for applications such as instruments in surgical kits and joint replacement trials. PPSU’s toxicological inertness also makes it viable for some Class II and III devices.
As with PEEK, the long-term stability of PPSU can significantly offset its initial material cost premium over lesser-performing polymers such as POM-C.
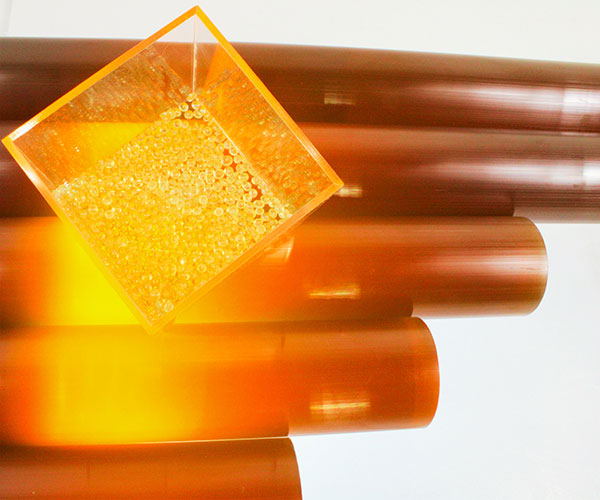
Glass-fiber Reinforced Radel® PPSU
Glass fiber reinforced Radel RG PPSU grades offer a significant increase in mechanical strength, structural rigidity and resistance to creep under load compared to unfilled Radel PPSU. They have been developed for medical device applications that must withstand extended exposure to high temperatures, hot water or steam while providing higher strength and stiffness beyond the limits of unfilled Radel PPSU.
For example, Radel RG-5010 with 10% glass fiber reinforcement has approximately 40% higher flexural modulus than unfilled Radel R-5000. The 30% glass fiber reinforced grade designated Radel RG-5030 PPSU shows a more significant step up in rigidity with over twice the flexural modulus of unfilled Radel resin.
Both glass-reinforced grades of Radel PPSU are available for injection molding and as extruded shapes for machined parts. Resins are available in black, blue and bone resin colors. Applications include multi-use sterilizable surgical instrument handles where rigidity is an asset, as well as internal brackets and other structural components of electrical and electronic medical devices.
PEI (Polyetherimide)
Polyetherimide is most commonly known by its tradename, Ultem PEI. Among amorphous polymers it ranks among the highest on chemical resistance and withstands cleaners and disinfectants used in health care facilities. It also retains its rigidity at elevated temperatures. The resin has a dark amber transparent tint, and is available in off-white and custom colors.
Compared to PPSU and PSU, Ultem PEI offers very high structural strength and rigidity at high temperatures, but has less resistance to impacts.
Ultem PEI excels in retaining its properties after hundreds of sterilization cycles and has been specified for use in autoclave devices. It also withstands gamma and chemical sterilization. Typical medical and health care applications include components for respiratory devices and infusion pumps, and structural parts for radiation therapy and sterilization equipment.
PSU (Polysulfone)
Polysulfone withstands most forms of sterilization, though to a more limited degree in some compared to PEEK, PPSU and PEI, as Table 1 shows. Its resistance to steam sterilization up to 121oC (250oF) is excellent. However, the polymer may embrittle at higher autoclaving temperatures which tend to anneal the material.
In its basic form, PSU is transparent, with a very light tint. This feature along with its sterilizability, chemical resistance and toughness has led to decades of use for heart valve sizers, dialysis filtration cartridges and pharmaceutical filter housings.
Like PPSU, polysulfone can be custom colored to differentiate instruments and medical procedure devices.

PARA (Polyarylamide)
Developed for single use healthcare applications, Solvay’s Ixef PARA features high strength and stiffness, and an exceptionally smooth surface. In injection molded instruments and devices, it is a cost-effective alternative to metals. Reinforced with glass fibers, it imparts exceptionally high rigidity to hand-held instruments.
On aesthetics, Ixef PARA molded parts maintain a high gloss surface finish, unlike many other fiber-reinforced plastics. Standard gamma-stabilized colors are based on an FDA Master Access File (MAF) supported color palette and allow easy visual differentiation of instruments.
PARA withstands several common sterilization methods (Table 1), and shows no significant change in appearance or loss of mechanical properties after exposure to gamma radiation.
Ixef PARA machinable semi-finished shapes
A common misconception is that Ixef PARA only serves injection molded applications. Genesis has developed the technology for extruding an array of rod and plate sizes for precision machined production parts as well as for machined prototypes for testing prior to injection molding.
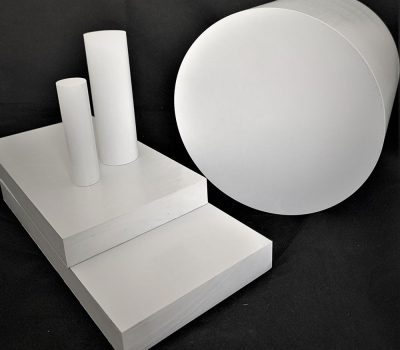
POM-C (Polyoxymethylene; Copolymer Acetal)
Commonly referred to as acetal copolymer, POM-C can withstand standard autoclave cycles at 121oC (250oF) in devices that have no significant load applied. It also exhibits very low moisture absorption and maintains its dimensions after steam sterilization.
The practical life of autoclaved POM-C components is usually limited to a few hundred cycles, and discoloration will occur. For this reason, Radel PPSU, with its superior color stability, has replaced POM-C in color-coded instruments and joint replacement trials. POM-C can be sterilized for a limited number of cycles in ETO and plasma, but gamma sterilization will cause it to degrade and embrittle.
There are a number of medical devices where POM-C’s physical properties, sufficient tolerance to the sterilization protocol and the advantage of low material cost make it a good option. Insulin pens are an example.
PC (Polycarbonate)
Transparent polycarbonate offers optical clarity, rigidity, exceptional toughness and the requisite biocompatibility for devices where visibility of fluids within the device is important. It is used in injection molded components for arterial filters and blood oxygenators and in machined valve bodies for laboratory and pharmaceutical where its transparency is an asset.
Polycarbonate is prone to degradation in steam, and therefore cannot be used for applications requiring autoclaving. It is compatible with gamma radiation, ethylene oxide gas and vaporized hydrogen peroxide.
PP-H (Polypropylene homopolymer)
Polypropylene homopolymer, or PP-H, combines broad chemical resistance, low moisture absorption and hydrolysis resistance. Heat-stabilized PP-H is often specified over the unmodified polymer for healthcare applications where higher temperature resistance is desirable for sterilization or in use.
Precision-machined or injection molded PP-H components can withstand up to 800 steam sterilization cycles, but the polymer can discolor and exhibit color changes typically around the 200 cycle mark.
Typical applications where its properties and cost make it an attractive candidate include oxygenator components, trays and clinical and laboratory instrument holders.
Genesis Support on Production Options and Materials
Genesis provides medical device manufacturers with the capabilities to transform the polymers they specify into the semi-finished machinable shapes and machined or injection molded components they require. Our ability to engineer equipment and develop process conditions for the most challenging material compositions has gained the recognition of MDMs, major resin producers and medical polymer compounders.
With over 25 years’ experience in high performance polymers and applications, our technical team helps designers narrow the field of material candidates. In-house services also include parts prototyping and ASTM physical properties testing of materials to help designers validate material options for their device components.