Historically, health care facilities used metals or premium high-performance biocompatible plastics for surgical instruments that could be sterilized after each use. More and more, however, hospitals see single-use medical instruments as a better way to safeguard patients from the risk of hospital-acquired infections (HAIs).
This trend creates the need to manufacture many more single-use instruments to satisfy higher demand and minimize the impact on health care costs. These factors give plastics a major edge over metals.
Another advantage of plastics, also termed polymers, comes with the new biocompatible grades that have been developed specifically for single-use surgical instruments. They offer biocompatibility and cost less than traditional high-performance plastics traditionally used for multiple-use instruments. They also have several advantages over metals.
How do plastics help satisfy higher demand for single-use surgical instruments?
The injection molding process for plastics turns out high quantities of items in very short production cycles. An individual multi-cavity mold into which melted plastic is injected yields several pieces in a single, fast operation. As a result, injection molding of plastics delivers a low cost way to produce high quantities of instruments very quickly compared to metal production methods.
Are there alternatives to injection molding plastics for low quantities?
Machining medical instruments and device components from extruded plastic rods or plates serves as a good option if production quantities do not justify building an injection mold. Extrusion as a manufacturing process is highly efficient. Biocompatible thermoplastics can be converted into machinable rods and plates by this form of melt-processing. High-speed CNC machining then converts the extruded shapes into plastic parts.
What are plastics’ benefits when used for surgical instruments?
Plastics offer several beneficial attributes for surgical instruments compared to metals. Their inherent characteristics help minimize hand fatigue, especially important during extended procedures. For example, plastics weigh far less than metals, so they are more user-friendly to handle. At the same time, biocompatible or medical grade plastics formulated with special additives offer high rigidity. This eliminates any concerns about instrument stability during operating procedures. Their strength properties in fact compare favorably to aluminum. Injection molding also allows easy one-step production of complex designs that promote better ergonomics. Metal instruments, conversely, usually require more costly finishing steps. Taken together, the benefits of plastics can add up to more cost-effective comfort and less fatigue in use.
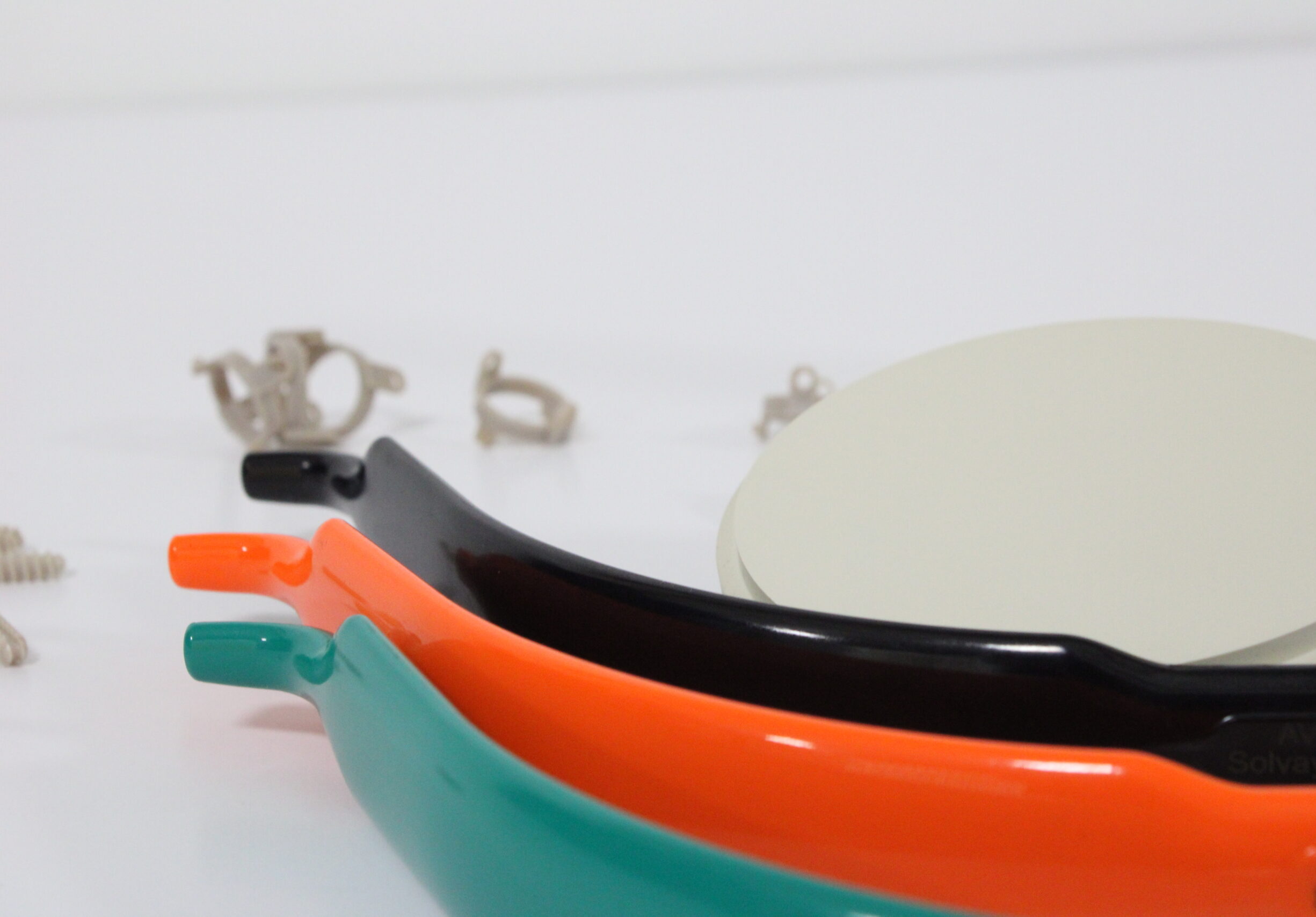
Plastics manufacturers can add an array of custom colors to these biocompatible polymers. This feature allows similar-sized instruments in the surgical suite to be differentiated by color. The color remains permanent because the plastic producers integrate it into the polymer while it is being made.
What biocompatible plastics are used for surgical instruments?
Plastic manufacturers have developed several materials that they offer as biocompatible grades. They are often called medical grade plastics. Certain formulations of Radel PPSU, Ultem PEI, acetal, polycarbonate and Ixef PARA number among these types of polymers. An advanced plastic with the designation PEEK has even gained wide acceptance as a material that meets the rigorous requirements for use in implantable device applications.
Why are there so many different medical grade plastics?
The polymer chemistry behind certain plastics gives them properties that provide long life for multiple-use instruments and devices. The different high-performance biocompatible polymers resist different chemicals. They resist corrosion and maintain their performance and aesthetics after repeated exposure to sterilization in steam, aggressive chemicals and gamma radiation. Typically, these polymers cost more to produce than general purpose plastics such as polyethylene and polypropylene and they carry a premium price. However, their longevity makes them a good value for multiple-use surgical instruments and a range of other medical devices.
What plastics are best for single-use instruments?
Most premium or high-performance medical plastics are over-engineered for single-use applications. The growth in demand for these devices and instruments has motivated plastic producers to develop materials suitable for these applications at an attractive price point. A notable example is Ixef PARA, a biocompatible polymer that Solvay developed specifically for single-use instruments and medical devices.
What kind of plastic is Ixef PARA?
Chemically, Ixef is a member of the polyarylamide (PARA) family. Solvay, an international plastics producer, manufactures the polymer. The semi-crystalline structure of the material gives it good inherent strength and chemical resistance. Specific medical grades are made for single-use instruments and devices.
Why is Ixef PARA a good choice for single-use applications?
Ixef PARA offers benefits in performance, cost, design, durability and aesthetics that make it a good choice for single-use surgical instruments and related medical devices. Specific features that make Ixef a good option for a variety of medical applications:
Ixef PARA resists deforming with strength properties that rival aluminum.
During the process for producing Ixef PARA polymer in pellet form, Solvay blends it with 50-60% glass-fiber reinforcement, depending on the grade required. The fibers significantly boost the material’s rigidity. Because they are integrated into the plastic itself, these fibers do not appear on the surface of the instruments or detract from their physical appearance.
The resulting tensile and flexural strength of Ixef give surgical instruments a level of rigidity similar to aluminum. In fact, the fiber-reinforced polymer’s strength exceeds that of some grades of aluminum. Its reinforced composition also makes the material highly resistant to deformation under pressure for extended periods, even at 120oF (48.9oC).
A clean, uniform surface and custom colors add up to medical-quality aesthetics.
It would be hard to find a high-strength polymer that comes close to the surface finish of Ixef PARA when injection molded. Parts come out of the mold with a uniform, high-gloss appearance.
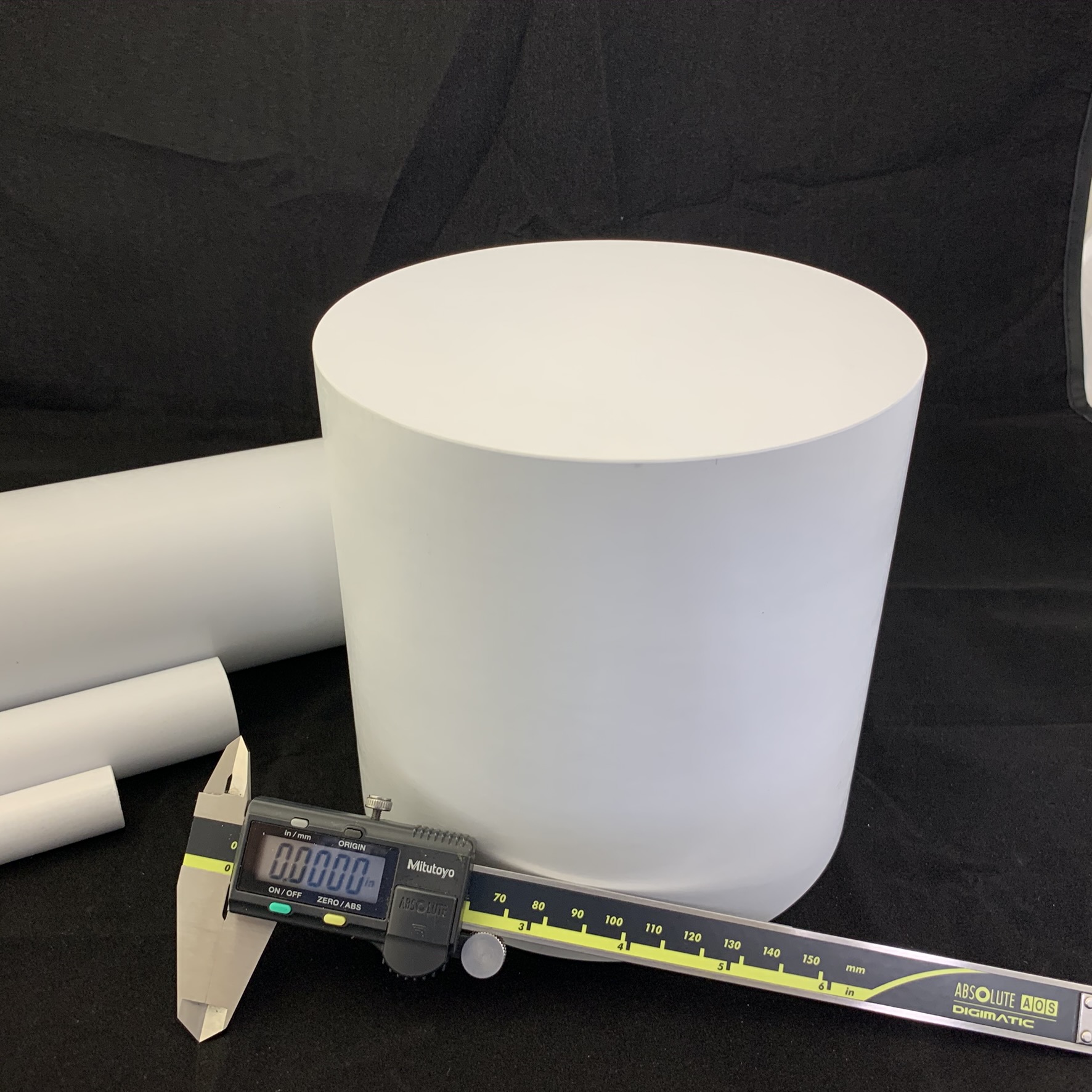
Instruments and device components machined from extruded Ixef rod or plate have a clean, uniform matte surface. The quality conveyed by the aesthetics fits well within a clinical or surgical environment.
Another advantage of Ixef over metals is that the polymer can be custom colored. This feature offers the ability to clearly differentiate instruments of a similar size during surgical procedures. Solvay integrates gamma-stabilized pigment into Ixef polymer during production. This ensures that the color remains inherent in the material and retains its integrity for the life of the device.
Surgical instruments designed in Ixef PARA provide ergonomic advantages.
Instruments and devices made from Ixef weigh far less than those made from metals, without compromising the required rigidity. As a plastic material, Ixef also allows complex ergonomically-friendly designs to be easily molded into each part. These attributes allow improved ergonomics in the operating environment that can reduce manual fatigue and lessen the risk of repetitive strain injuries.
Ixef resists a wide spectrum of clinical and hospital chemicals and cleaners.
Most solvents, including hydrocarbons, ketones, ethers, esters, chlorinated solvents, and glycols pose no problem for Ixef PARA. The polymer also resists degradation and loss of properties when exposed to cleaning fluids and many aqueous solutions.
A related benefit of Ixef is its very minimal dimensional change when immersed in water for extended periods.
What are typical healthcare applications for Ixef PARA?
The diverse single-use surgical applications of Ixef include operating instruments such as inserters, curettes, needle holders, forceps, retractors, and extractors. Single-use spinal surgery kits utilizing Ixef for various components enhance operating room efficiency. These kits also eliminate reprocessing costs, and factor into reducing surgical site infections.
Who can convert Ixef PARA into finished components?
As a melt-processable thermoplastic, Ixef PARA can be injection-molded into components for instruments and devices. However, its exceptionally high level of fiber-reinforcement means it requires an injection molding company that has experience and the process control system needed for highly-filled formulations.
What expertise and equipment are needed for injection molding Ixef PARA?
Different polymers and the various formulations of the same polymer react differently during melt-processing. Their fundamental chemistry and compositions cause these differences. The glass-fiber reinforced grade of Ixef PARA for medical applications, for instance, is a good example. It requires a much different temperature and pressure profile during injection molding compared to unfilled or “neat” PARA. These differences call for expertise in how the material behaves under specific temperatures and pressures. It also requires highly accurate process control systems for monitoring and managing these variables to ensure the polymer doesn’t degrade.
A capable, certified injection molder will have the expertise and resources needed. Their experience and the right process control technology will help ensure that every molded product has the optimum performance and consistent quality the healthcare industry demands to avoid unnecessary rejects and waste. These capabilities also ensure efficiency and the reliability of a dependable supply chain.
What if a customer requires Ixef PARA with proprietary or custom additives?
Proprietary formulations typically require that the unfilled Ixef PARA is supplied to a qualified compounder who can produce the required custom grade. The custom formulation then moves to the injection molder for conversion into components.
Experienced injection molders have close relationships with specialized companies and can facilitate this step. They can source and work with a qualified compounder, coordinate the supply chain and manage it through to final production and delivery of finished Ixef PARA components to the customer.