Medical device manufacturers rely on prototyping to convert a concept into a material form that gives designers, engineers and the marketing team an important first look at a potential product. As the project moves forward, prototypes then facilitate multiple aspects of the device development process.
From early proof-of-concept alphas to near-final pilots, MDMs typically will refine a device prototype many times. This makes it important to have a prototype manufacturer with experience in different medical plastics, and the ability to make design changes quickly to keep projects moving forward.
Typical Steps in Developing and Commercializing a Medical Device
The development of a medical device typically follows these tracks:
- Product design development and prototyping
- Usability engineering and human factors
- Intellectual and property management
- Risk and quality management
- Manufacturing
- Regulatory compliance
Design and Prototyping Facilitate Other Steps
Product design and prototyping are inter-related as a stage of device development that supports and enables every other developmental track. As a medical device or product evolves from concept to full production, its prototypes will also evolve from proof-of-concept to a product configuration that approximates the final device.
Prototyping Stages and Where They Fit in the Development Process
Prototypes enable a device’s design to be tested, refined with any required modifications, and finally validated. The ability to modify prototypes quickly for testing through the stages of the development process is an important consideration in choosing a method to produce them.
While validation steps required for commercialization might vary somewhat for different types of devices, the following prototyping stages are typical:
Alpha prototypes
These are produced after the development team has gathered enough information to define the initial design for a device. Inputs for this step come from the initial product concept designs and drawings or models, research into its uses and benefits, interviews with potential end-users, risk management studies, and analyses of devices or products with which the new device is intended to compete or displace.
The essential roles of an alpha prototype are to confirm feasibility, finalize product dimensions and identify potential safety or efficacy risks. To do so, they are tested in controlled laboratory environments, and the need for any design iterations as signaled by the results are quickly implemented.
In some instances, additional proof-of-concept prototypes may be needed during the early stages of product development. These prototypes may be used to demonstrate basic feasibility and design, and serve as physical examples for project funding and budgeting purposes.
Beta prototypes
The primary difference between alpha and beta prototypes is that alphas are developed in-house as the basis for the conceptual design, while betas are sent to users for feedback that can define opportunities or requirements for design improvements. They incorporate data gathered during the alpha phase, then are designed, produced and refined based on end-user feedback and extensive testing. As such, beta prototypes are a key step in optimizing all aspects of the final device.
Pilot prototypes
At this stage of product development, pilot prototypes replicate the final design and function of the device, and are made from the specified material in the manufacturing process intended for full production. They can be used in clinical trials or even as part of an initial product rollout.
Most MDMs will also utilize pilot prototypes to make and test design improvements based on user feedback, to generate clinical test data, and to complete V&V.
Any changes at this point constitute relatively minor refinements, as the device has taken on its final design and aesthetics. Regulatory submission and manufacturing validation are also typically done at this point using the pilot prototypes.
How Prototypes Support the Product Development Process
Prototyping impacts every other phase of the medical device development process. Specifically, it will influence the following:
Material selection
MDMs have an array of options in medical grade plastics, each with its own physical properties, sterilization and chemical resistance, and biocompatibility characteristics. Prototyping lets the design team test and evaluate a device made from different material candidates for their application. This versatility allows designers to pinpoint the medical plastic that offers the best balance of physical performance and cost-effectiveness.
Production methods
- CNC machining: If the device has complex geometries or if certain surface finishes are required, machining parts from extruded semi-finished shapes may be the manufacturing process of choice. Machining is also well-suited to lower unit volumes that do not justify the cost of injection molding tooling.
- Injection molding: For high volume production where machining highly complex features is not required, injection molding is usually the best option. High unit volumes justify the investment in production tooling, and turn-around time for producing parts is very fast.
-
Injection molding near-net shapes (approximate size blanks) then finish-machining to exact dimensions is an efficient way to produce higher quantities of prototypes market testing before investing in production molds. Near-net shapes: A transition step between lower production quantities typical for machining and higher volumes associated with injection molding involves near-net shapes. Essentially injection molded blanks, near-net shapes closely resemble the desired part. Eliminating the need for exact dimensions and tolerances allows the use of low-cost tooling. An efficient finish-machining operation then achieves exact design dimensions. The combination of economical injection molds plus machining with minimal material loss can make this an attractive step until volumes justify an investment in full-production injection molding tooling.
Usability testing
Late-phase prototypes offer MDMs an opportunity to have end-users evaluate devices that are planned for commercialization. This can provide useful feedback for improving a medical device’s design and its functionality. User-testing of prototypes can also help validate the specified material’s compatibility with the conditions and environment in which it is planned for use.
Risk management
Prototype testing allows the design team to identify and isolate potential faults in the device’s design Risks can then be assessed for their probability and likely severity. Beyond the obvious benefits of protecting end-users and as well as preserving the manufacturer’s reputation, the ability to assess and manage risk that prototype testing affords will also expedite regulatory compliance.
Product design
Prototype testing is a cost-efficient way to identify areas where a device’s design could be – or may need to be – improved. Rapid prototyping by machining or other methods can also be used to evaluate materials and design configurations that could affect performance attributes, such as user comfort, functionality, and longevity in different sterilization procedures.
In summary, prototyping can help confirm critical development decisions on the optimum design, material and manufacturing approach for the device. Prototypes can also facilitate the steps toward regulatory compliance, and provide the market feedback that indicates the likelihood of achieving commercial goals.
What Are The Typical Ways To Make Prototypes From Medical Grade Plastics?
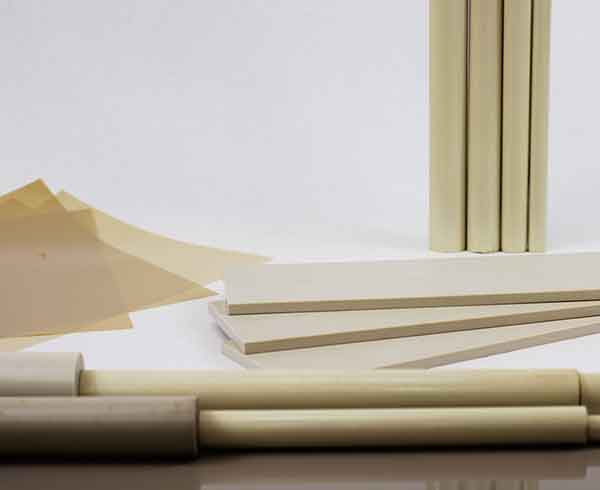
Fast turn-around times and low cost for modifications are important criteria for producing prototypes, especially in the early stages of development. Low quantities for testing and performance validation are also the norm at this point. Machining semi-finished shapes is one commonly used method for making prototypes that measure up well against these qualifiers. Another is 3D printing, also referred to as additive manufacturing.
As projects get more defined, near-net shapes or rough blanks that are injection molded in low cost tooling and finish-machined to specifications become an attractive option, especially when higher quantities are needed for broader user evaluations or market testing.
Choosing a Prototype Manufacturer
With machined prototypes, consistent performance and quality starts with how the semi-finished shapes are processed. This is because process conditions for a medical plastic can affect the performance of the device itself. For example, excessively high melt temperatures can degrade the “data sheet” toughness of a medical thermoplastic, resulting in brittle finished parts.
A semi-finished shapes processor specializing in medical plastics and having its own machining operation can be an ideal choice. Such companies can offer the processing and machining expertise to deliver prototypes with the consistent performance and quality required for market testing and for regulatory submittals. Similarly, a specialist in extruding shapes in medical grade plastics can be a technical asset to an independent machining company or an MDM’s internal prototyping operation.
The importance of maintaining the right melt process profile specific to each medical grade plastic also applies to injection molding and to additive manufacturing or 3D printing. The essential point: optimal processing conditions translate to optimal performance in prototypes.
Another factor in selecting a prototype supplier is flexibility and responsiveness. As product testing and market feedback indicates the need or opportunity for design improvements, a prototype supplier’s ability to make changes quickly helps keep project schedules and commercialization target dates on track.