Home - Conversion Capabilities - Injection Molding Shapes & Components - Injection Molding Case Study: Solving Void Problems
During the early stages of a project to develop a new product, Genesis Medical Plastics was contacted by a medical device manufacturer to determine if we could resolve a problem with voids in injection molded parts. The customer’s goal was to design and produce innovative and more cost-effective implantable suture anchors. For orthopedic surgeons, these anchors are used for various procedures in different joint spaces. The devices were to be injection molded from an implantable grade of PEEK thermoplastic.
The initial injection molder was charged with injection molding near-net “blanks” which were then to be CNC-machined into two sizes of suture anchors.
It soon became evident to their machinist that far too many of these molded blanks contained internal voids which threatened the structural integrity of the suture anchors. This was entirely unacceptable, especially given load bearing, long-term implantable nature of these devices.

Application and material specified
Suture anchors are widely used for fixation in arthroscopic repairs, especially in rotator cuff (shoulder) and hip labrum repairs. They are available in various sizes and configurations, and when utilizing implantable PEEK thermoplastics, are typically injection molded or molded as blanks then finish-machined.
PEEK (polyetheretherketone) is a high-performance engineering thermoplastic characterized by an exceptional combination of properties. These properties range from structural strength and toughness to the ability to withstand aggressive chemicals and extremely high temperatures. The need to process the polymer at high melt temperatures and the tight process controls required for optimum properties and consistent quality can present obstacles for molders who lack extensive experience with the polymer or those who do not have the right molding technology.
The implantable grades of PEEK polymer commercialized under the Invibio brand and as Solvay’s Zeniva have been used successfully in many medical devices. The polymer is bio-inert and boasts a flexural modulus very similar to that of cortical bone, making it an exceptional choice for implanted orthopedic applications such as suture anchors.
Defining the problem areas
In melt-processing of plastics, internal voids in parts can be caused by several factors: improper process conditions or process controls; high moisture content in the material itself; or by the physical design of the part, typically related to non-uniform wall thicknesses or wall sections of 6.35 mm (0.25-inch) or more. All three conditions can be remedied.
For the suture anchors, the solution to voids required maintaining optimum process conditions for parts with relatively thick, non-uniform wall sections, which are design features necessary to achieve the intended functionality.
In these configurations, voids can occur when the outer area of the component cools and solidifies faster than the internal area. They can also occur when a differential in the wall thickness creates a different rate of cooling in thin vs. thicker sections of the part. This differential can create voids as the part cools. In actual use, these voids are weak spots that can negatively affect the ability of the parts to withstand physical load.
Developing the solution
While often visible in parts made from transparent plastics, identifying voids in opaque parts requires either destructive physical sectioning, or analytical imaging. Genesis’ analytical lab was able to scan the molded parts and determine the process conditions for implantable PEEK and any mold modifications necessary to eliminate voids.
The next step in quality assurance was to ensure that the optimum process conditions would be maintained. Genesis’ engineers designed and engineered our process control system with transducers installed within each mold cavity. The technology monitors and maintains the ideal pressures and temperatures for each polymer formulation, to ensure consistently high quality, uniformity and performance of every injection molding part produced.
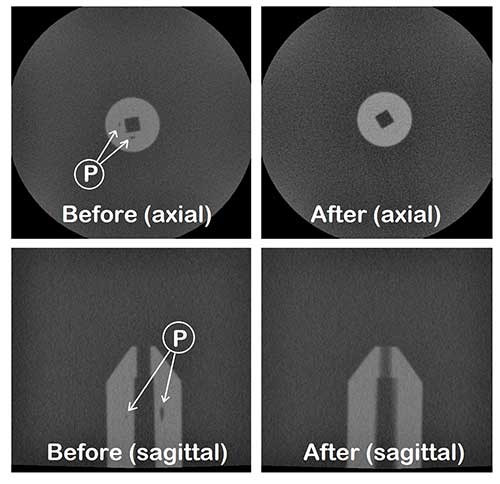
The outcome
Genesis routinely injection molds void-free suture anchor blanks and consistently meets the customer’s overall quality protocol for these implantable devices.
To maintain tighter quality control during every step of production, the customer has chosen Genesis to finish-machine the void-free injection molded blanks.
In addition to injection molding and precision CNC machining, our dedicated medical polymer conversion capabilities also include melt extrusion of machinable stock shapes. Customers routinely supply their implantable and medical grade polymer formulations to Genesis for production of finished parts as well as for extrusion into a wide variety of custom rods and plates for their own internal machining operations.